How do you design an industrial ventilation system?
- Identify contaminant sources
- Determine your air change rates
- Select a ventilation type
- Design the ductwork and exhaust systems
- Incorporate controls and monitoring
Overview
- Effective ventilation is essential for employee safety, operational efficiency, and regulatory compliance, especially in industries with airborne contaminants.
- Identify the sources of the contaminants, determine necessary air change rates, choose appropriate ventilation types, design efficient ductwork, and incorporate control and monitoring systems.
- General exhaust systems ventilate whole spaces, while local exhaust systems target specific pollutant sources, both working together to optimize air quality based on facility layout.
- Automated controls and sensors regulate airflow and monitor air quality, ensuring safe and energy-efficient operations by adjusting to real-time conditions.
Maintaining high air quality in an industrial environment is a safety measure. It’s a critical factor in ensuring operational efficiency and regulatory compliance. Poor ventilation can lead to the accumulation of airborne contaminants, which pose health risks to employees and result in equipment malfunctions. Addressing these challenges starts with a well-designed ventilation system tailored to your facility’s unique needs.
In this article, we’ll guide you on how to design an industrial ventilation system. From identifying the sources of contaminants to determining the optimal air change rates and selecting the appropriate ventilation type, we’ll break down each component to help you build a workspace that prioritizes both safety and compliance. With the right system in place, you can protect your workforce, improve operational performance, and meet regulatory expectations seamlessly.
Identify Contaminant Sources
Contaminants in an industrial setting can range from dust and fumes to chemical vapors and microbial particles. Each source of contamination affects air quality in distinct ways, and addressing them effectively requires targeted solutions.
Dust and fumes consist of airborne particulates that can settle on surfaces or be inhaled by workers, leading to respiratory issues. In contrast, chemical vapors pose more severe health risks and require specialized filtration systems to neutralize harmful substances.
By understanding the specific characteristics of each contaminant, you can ensure that your ventilation system is equipped to address each issue effectively.
Determine Your Air Change Rates
Air change rate refers to how often the air in a space should be replaced within an hour, ensuring that contaminants are effectively diluted and removed. Different types of spaces also require varying air change rates depending on their use and the types of pollutants present.
Calculating the right air change rate is key to maintaining a safe and comfortable environment without overloading the system or wasting energy. Here’s how to determine the correct air change rate for your facility:
- Consult industry standards: Guidelines from organizations like ASHRAE provide recommended air change rates for different industrial spaces. Following these standards ensures compliance and protects employee health.
- Assess contaminant concentration: Higher contaminant levels may require increased air changes. Measure and monitor the levels of each contaminant to adjust air change rates as needed.
- Consider space volume and usage: Calculate the cubic volume of each space and take into account the intensity of the processes occurring there. High-activity areas or enclosed spaces often require higher air change rates to maintain acceptable air quality.
Select a Ventilation Type
Industrial ventilation falls into two main categories: general and local exhaust. General exhaust systems are designed to ventilate entire spaces by replacing stale air with fresh air throughout the facility, making them ideal for diluting contaminants spread across a large area.
In contrast, local exhaust systems target specific sources of pollutants, capturing contaminants directly at the source to prevent them from dispersing into the surrounding workspace.
Choosing between these systems—or combining both—depends on the layout of your facility and the concentration of contaminants in various areas.
Design the Ductwork and Exhaust Systems
Properly designed ductwork ensures smooth airflow throughout the facility, efficiently transporting contaminants from their source to the exhaust point. This involves calculating duct sizes, airflow rates, and pressure requirements to minimize resistance and optimize air movement.
The placement and design of exhaust outlets are also just as important, they should be positioned to capture and expel contaminants effectively. For instance, placing exhaust points at high concentrations of airborne contaminants, like near machinery or chemical processing areas, maximizes pollutant removal and reduces exposure in occupied spaces.
With F.R. Sevilla’s expertise, you’ll have guidance on selecting and designing ductwork and exhaust systems that work in harmony to provide clean, compliant air quality in your industrial environment.
Incorporate Controls and Monitoring
Controls, such as automated dampers and variable-speed fans, help regulate airflow based on real-time needs, which reduces energy consumption and keeps operating costs manageable.
For example, automated dampers can adjust ventilation rates based on occupancy or air quality levels, while variable-speed fans allow for precise control over airflow in different areas. These adjustments help maintain optimal conditions without wasting energy, supporting both efficiency and compliance goals.
Monitoring systems are equally crucial because they provide continuous feedback on air quality and system performance. Sensors can detect pollutant levels, humidity, temperature, and airflow, alerting operators if adjustments are needed. This allows for proactive maintenance and rapid responses to air quality issues, preventing potential hazards.
Key Takeaway
Designing an industrial ventilation system requires a strategic approach that addresses the specific needs of your facility. By following these, you can create a system that protects both employees and equipment while maintaining regulatory compliance.
At F.R. Sevilla, we specialize in tailored industrial ventilation solutions designed to meet the unique demands of each workspace. With our expertise, we ensure that every aspect—from air quality control to energy efficiency — is thoroughly addressed. Reach out to us today to discuss your ventilation needs, and let us help you create a safer, more productive environment for your operations.
RECENT POSTS
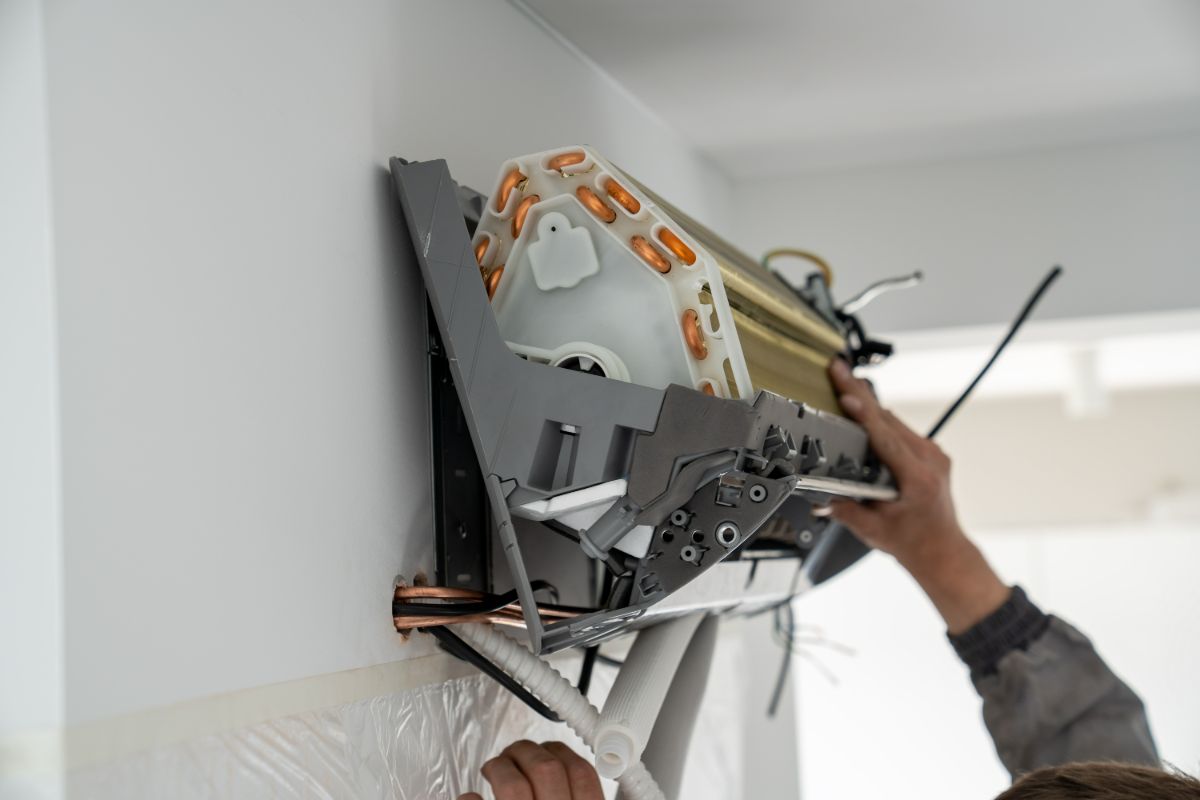
Your Guide to Finding the Best Air Conditioning Contractor in the Philippines
What should you look for in an air-con contractor? Licenses and certification Experience and reputation Insurance and wa
Read More
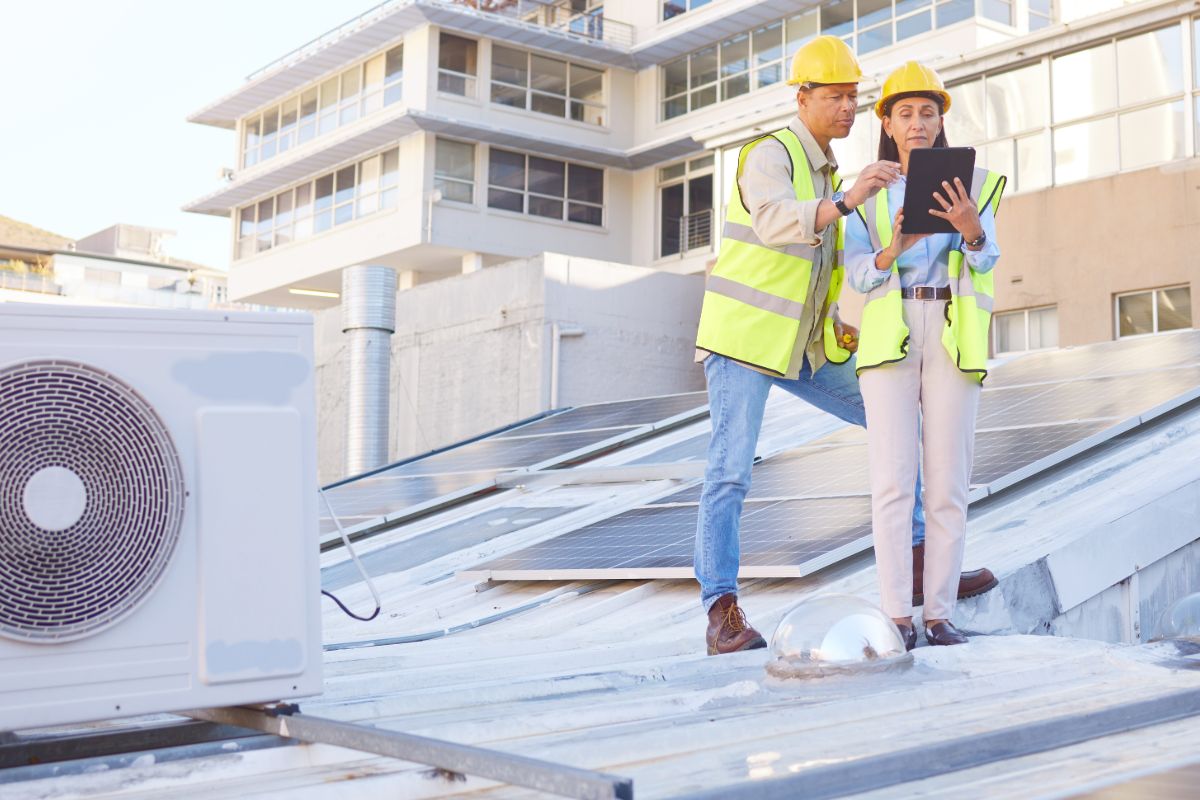
What to Expect from Air Conditioning Contractors?
What can you expect from air conditioning contractors? Comprehensive site assessment Professional installation and testi
Read More
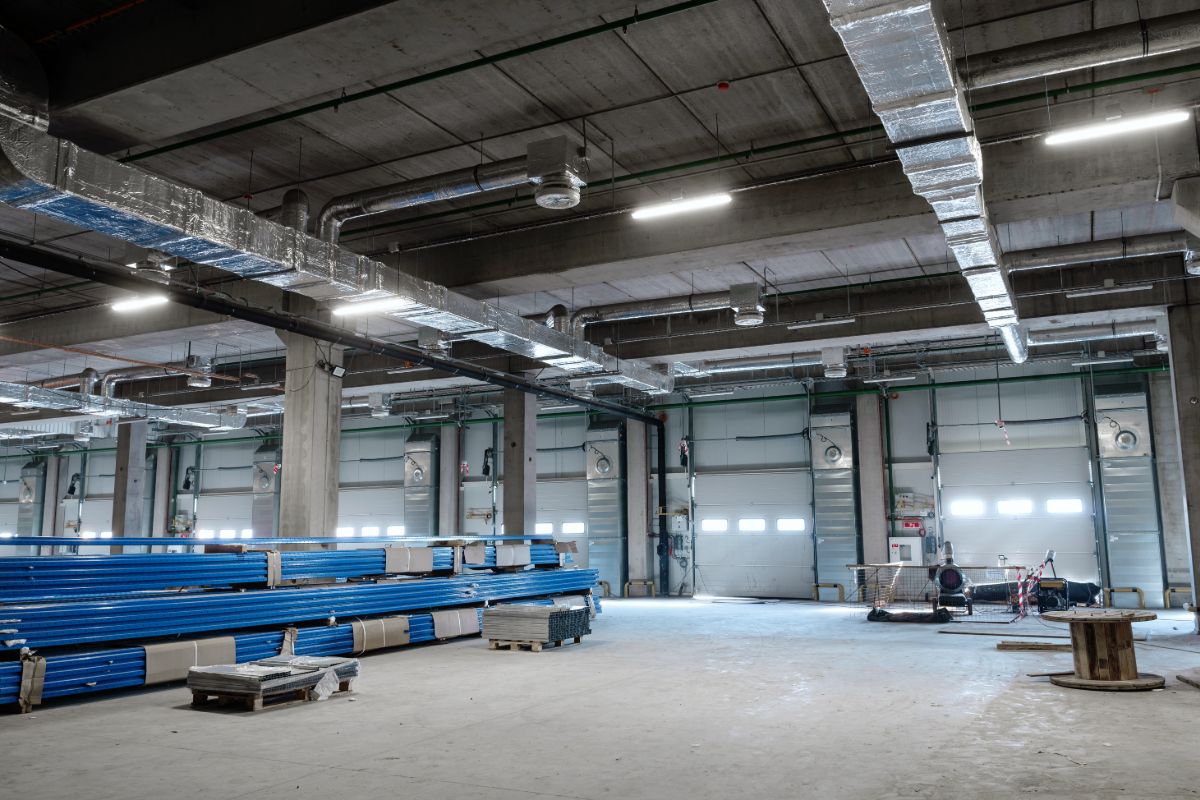
Cut Costs, Not Corners: Energy-Efficient Warehouse Cooling Solutions
What are the benefits of energy-efficient cooling solutions for warehouses? Lowers energy costs Improves employees produ
Read More